- This intricate and exclusively handcrafted block-printing technique came to Kutch from Sindh some 400 years ago at the behest of the King of Kutch, who invited craftsmen from Khatri community to come and practice their art on the banks of Dhamadka river. A large part of the credit of this art's revival goes to Dr. Ismail Mohamed Khatri, who has been acclaimed internationally as a master craftsman of the traditional Ajrakh, a craft that can be traced back up to ten generations in his family. His son, 40-year old Sufiyan Khatri, continues the legacy and is known for crafting the amazing two-sided printed Ajrakh, using an ancient technique that has remained unchanged over the last millennium.
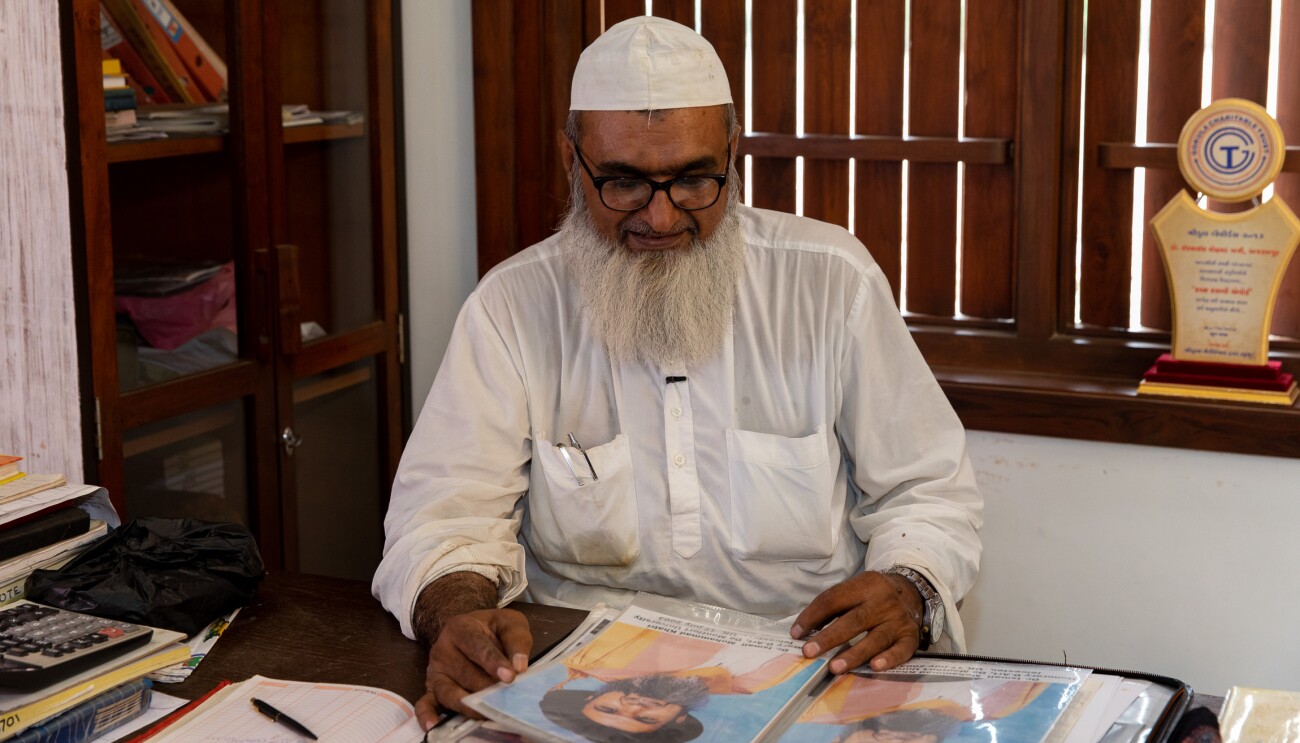
2. The popular story among local practitioners is that Ajrakh means “keep it today.” The cloth is made in a sixteen step process of washing, dyeing, printing, and drying, with one step being performed in one day and the fabric being put to rest for the day.
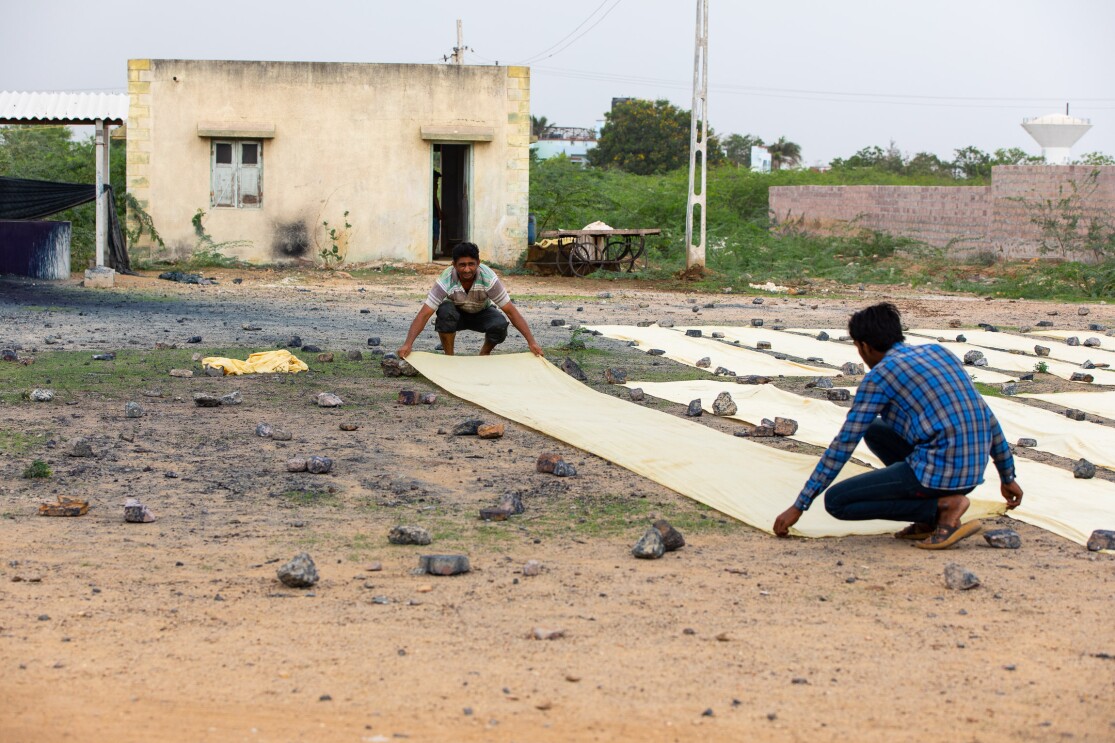
3. The ingredients for Ajrakh are all derived from nature, be it herbs and vegetable essence or natural minerals. Some of the common ingredients are wild indigo, pomegranate bark and seeds, and harde. Camel dung, found abundantly in the region, is used as an ingredient to remove starch from the fabric.
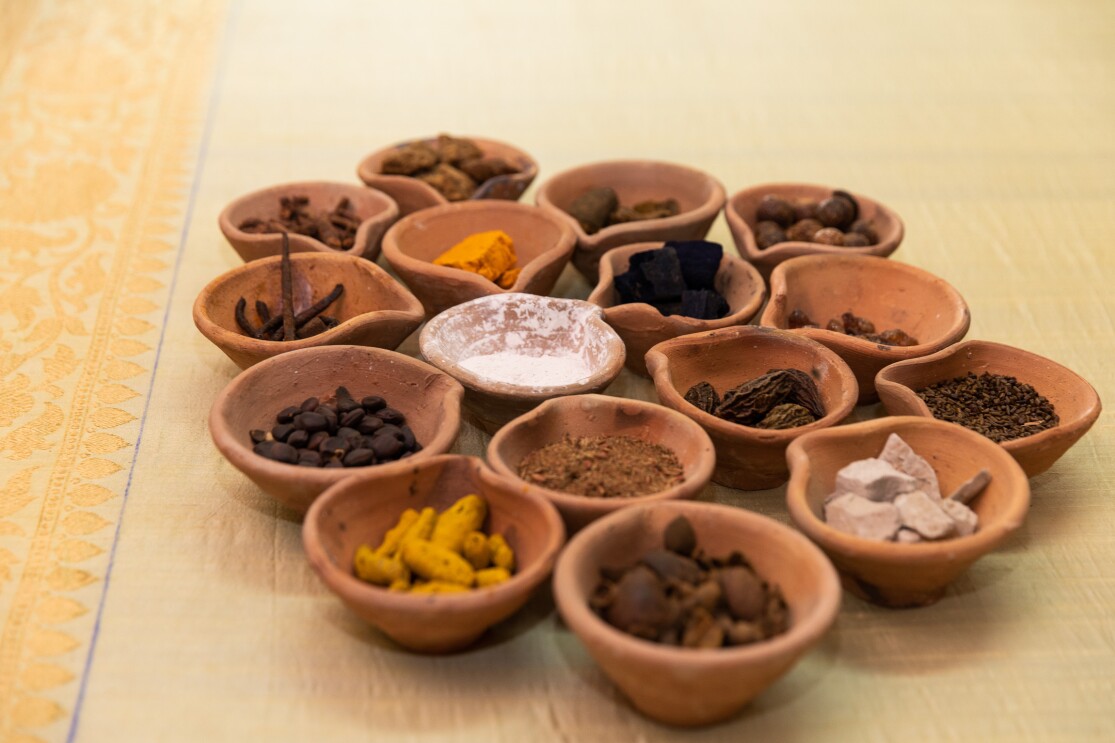
4. It is hard to believe that the artisans use rusted iron to create dye! Scrap iron, jaggery and tamarind is soaked in water for two weeks and then cooked over flame to create the black dye for Ajrakh.
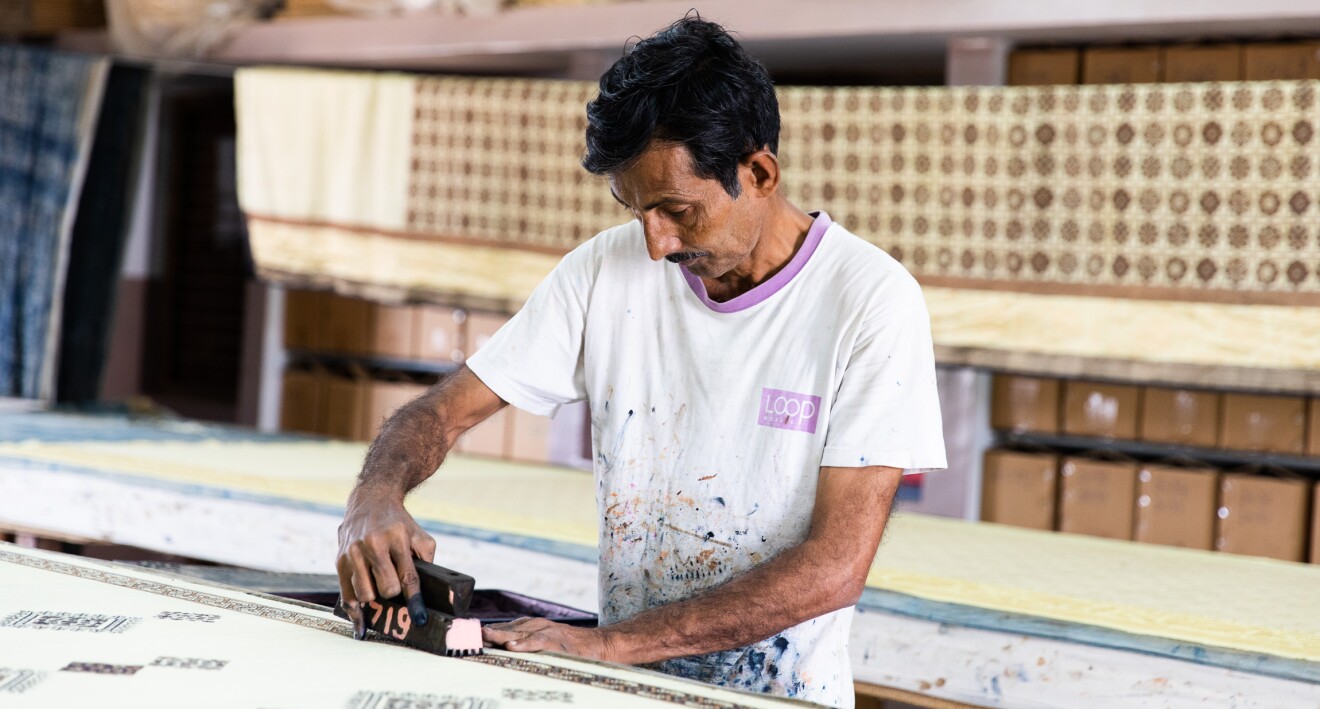
5. The natural dyes used in Ajrakh printing lends a unique characteristic to the fabric. During summers, it expands the pores of the fabric, making it easy for air to pass through. During winters, the pores of the fabric close, providing warmth. No wonder, they say that Ajrakh is suitable to wear around the year.
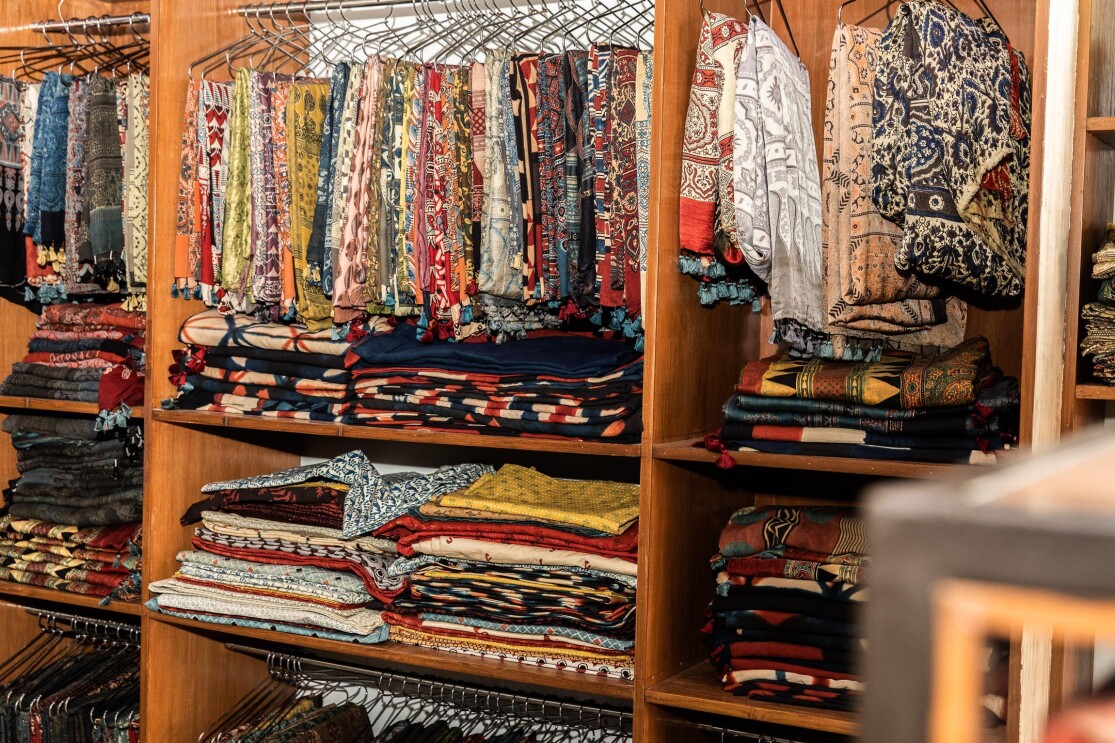
6. Historically, Ajrakh has been printed on both sides. This is because the cattle herders, who used to wear Ajrakh traditionally, would leave their homes even before sun rise and there was no electricity in those times so they couldn’t differentiate the right side from the wrong side in darkness. Double-side printing ensured that they could wear it either ways.
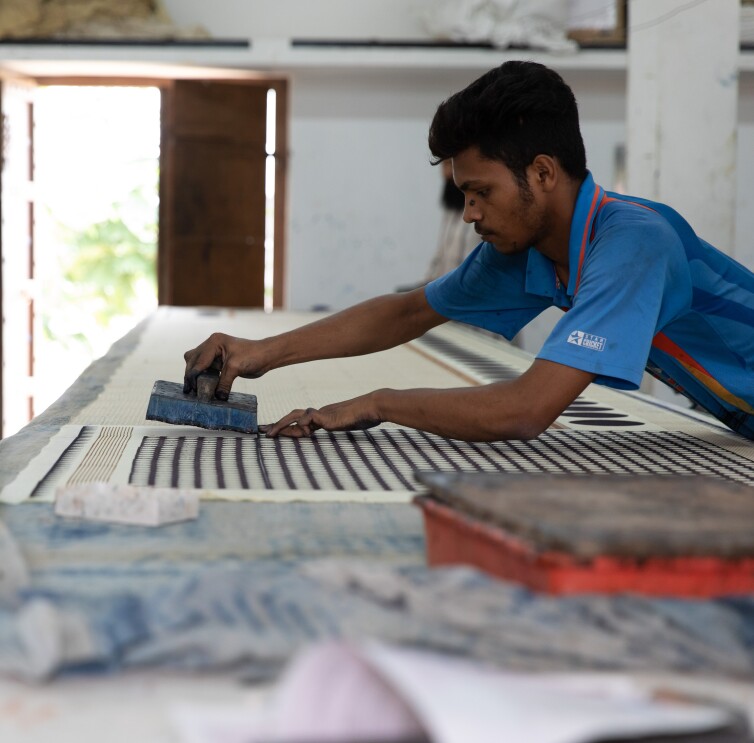
7. Ajrakh is colourful and bright for a reason. It was not just cattle that could get lost in the white desert. It was not uncommon for cattle herders to lose their sense of direction in the endless sands of desert. Bright colours made it easier for others to locate them even at a distance.
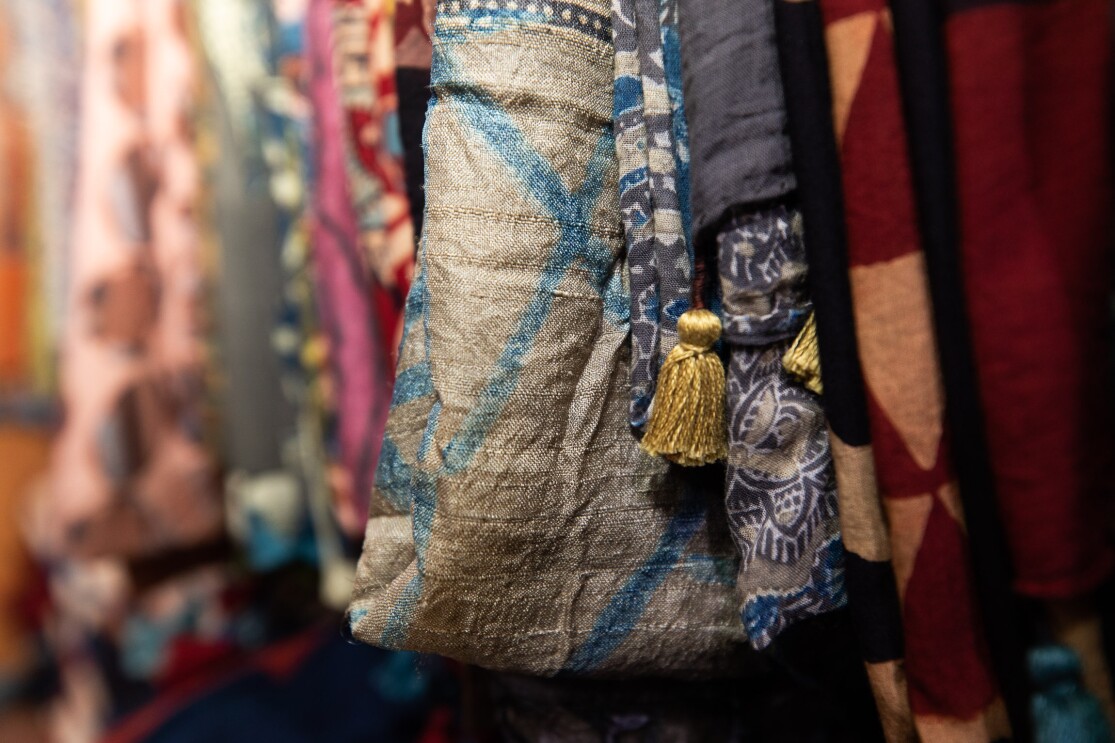
8. Water plays an essential role in the process of dying and the quality of water is as important as the quantity. If the water is high in minerals, the colour and concentration of the dyes is affected.
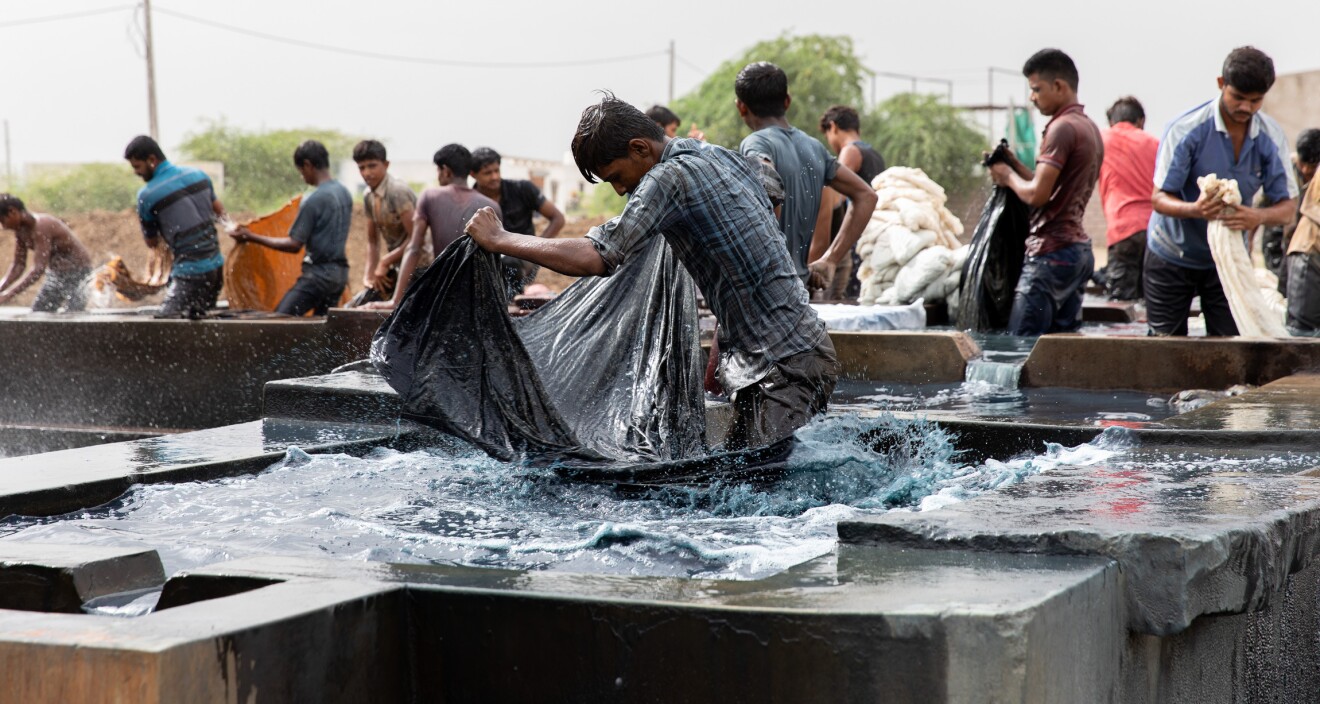
9. The wooden blocks used in Ajrakh printing are traditionally being carved by experts. Now, many artisans have mastered the art of chiseling teak wood blocks themselves in complex geometrical and intricate floral patterns.
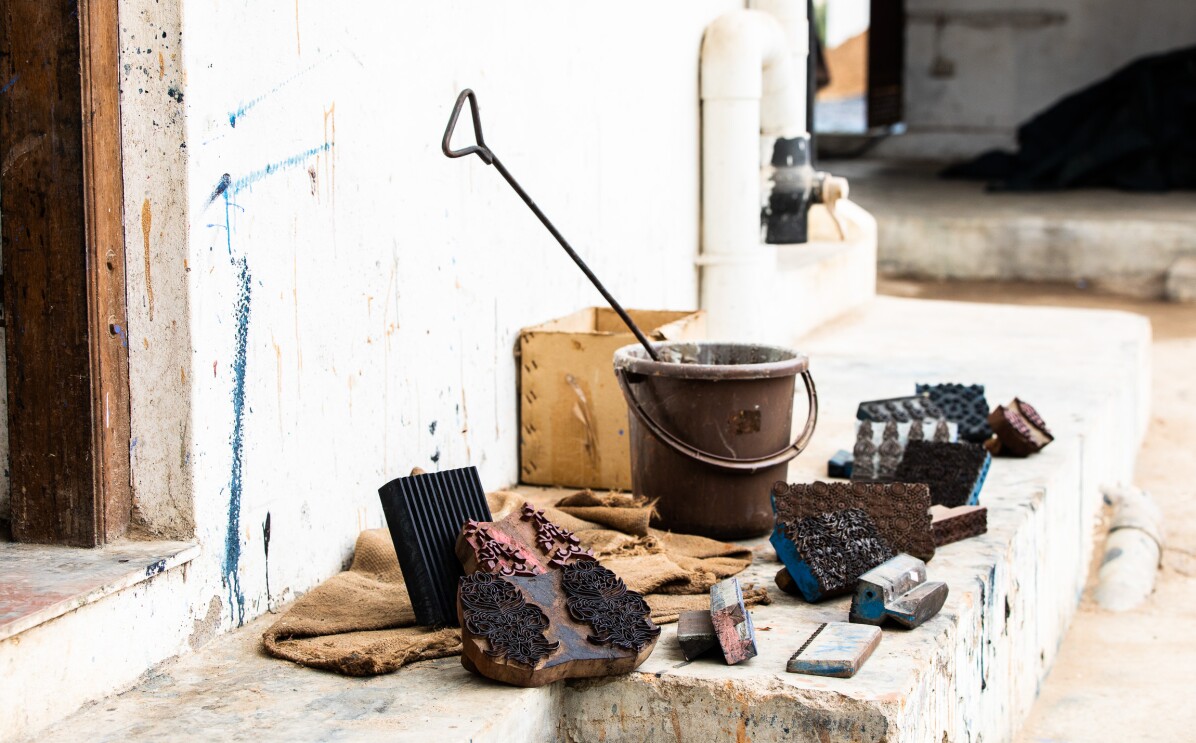
10. It is said that all the beautiful things found in the world inspired the artists to come up with ideas for the Ajrakh blocks. It’s not uncommon to find designs of clouds, rain drops, stars and moon.
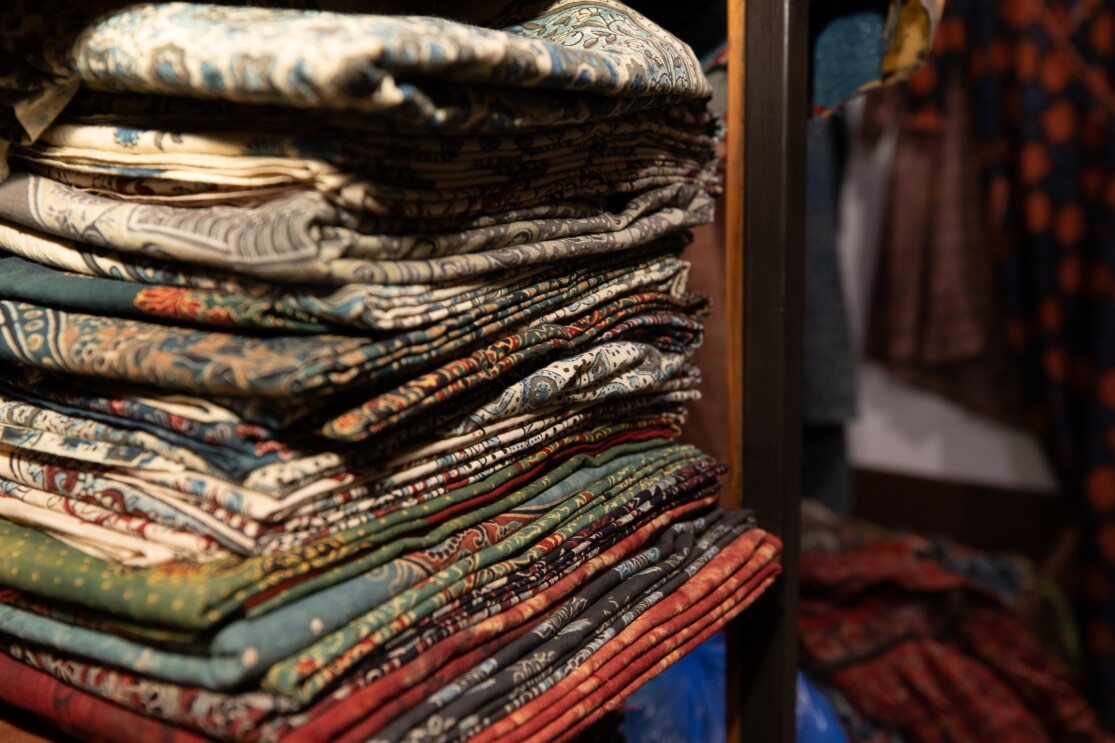
11. While traditionally Ajrakh was worn only by men from the pastoral community of the Kutch, today it has become a fashion statement for the affluent buyers, both men and women, looking for organic, ethical fashion.
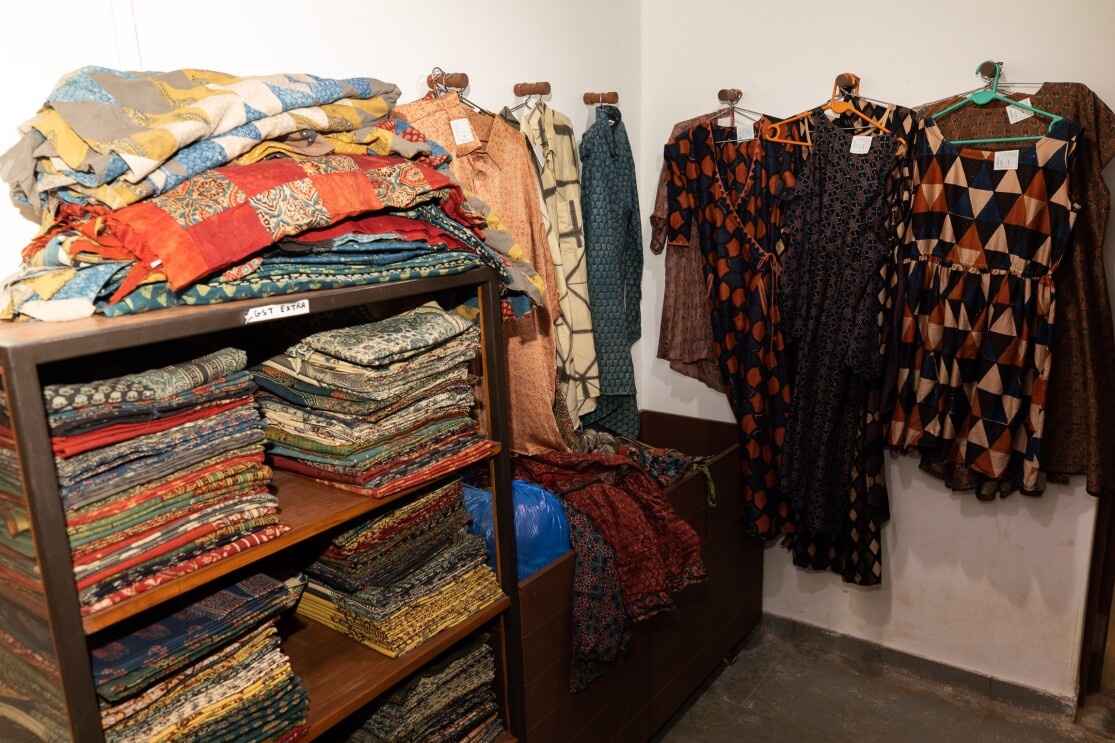
12. The 16-step process required to create a piece of Ajrakh fabric is what makes the outcome so beautiful and intricate.